One standout project is the 400-hectare Prodezi Eco-Industrial Park (IP), which is slated to hand over its first phase to tenants by the third quarter of this year.
The park is being developed under the government’s visionfor eco-IPs, aligning with global trends in green and sustainable development.
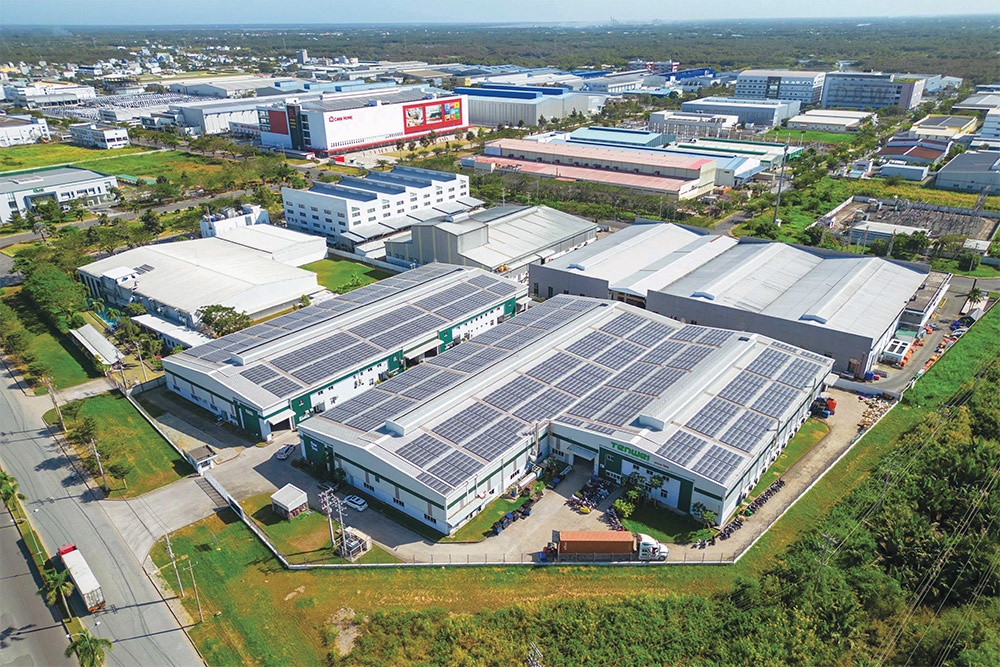 |
New standards being reached within green industrial parks |
According to Huynh Van Son, Vice Chairman of Long An People’s Committee, Prodezi not only meets high technical infrastructure standards but also pioneers the eco-industrial model in the Mekong Delta region.
“Adjacent to the LA Home eco-urban area, Prodezi Eco-IP represents a bold move towards integrated, sustainable industrial development in southern Vietnam,” Son said.
With an investment of over $195 million, the park is built on four core pillars: the use of renewable energy, water recycling and reuse, the development of green-certified buildings, and the preservation of biodiversity. Solar energy systems and energy-efficient technologies are being deployed to reduce CO2 emissions, targeting carbon neutrality in the long term.
Water recycling systems will help reduce environmental impact by minimising resource extraction and pollution, while buildings in the park will meet international green building standards, optimising energy use and employing environmentally friendly materials. The project also prioritises biodiversity conservation through the creation of green spaces and protection of natural ecosystems.
Meanwhile, KCN Vietnam last year formally announced its commitment to more green buildings, aligning with global standards to create more energy-efficient, environmentally friendly industrial facilities.
Since then, it has broken ground on two key projects – DEEP C Haiphong and Nhon Trach in Dong Nai, both designed and constructed with the goal of achieving LEED Gold certification, as set by the US Green Building Council.
Hardy Diec, CEO of KCN Vietnam, which currently operates and develops over 300 hectares with 10 industrial and storage warehouse projects nationwide, said the company integrates green building principles throughout the entire lifecycle of its projects.
“This includes of optimising energy performance through innovative energy management systems, enhancing water efficiency, prioritising sustainable materials, and reducing environmental impact by using recycled construction materials and minimising demolition waste,” Diec said.
Diec explained that global supply chain shifts and the drive to diversify manufacturing bases have accelerated demand for high-quality industrial infrastructure in Vietnam.
However, he stressed that to maintain momentum in foreign investment, industrial real estate developers must go beyond simply offering warehouse space. Instead, they need to build comprehensive ecosystems that enable companies to establish and expand operations safely, efficiently, and sustainably.
“We plan to ramp up investments to expand its land bank across key economic zones, providing investors with more flexible options while continually upgrading construction quality in line with sustainable development standards,” he said.
Meanwhile, Singaporean developer Sembcorp and its Vietnamese partner Becamex IDC is actively expanding the Vietnam-Singaporean Industrial Park (VSIP) portfolios to 20 integrated townships and IPs across Vietnam, covering 12,000ha.
In March, the two sides signed an MoU for four prospective VSIPs in Haiphong city and the provinces of Hung Yen, Hai Duong, Binh Duong, and Thai Binh.
VSIP III, located in Binh Duong, commenced operations in 2024. Spanning 1,000ha, the park is designed as a green and smart industrial hub, incorporating renewable energy systems and sustainable infrastructure.
The facility utilises solar power as an alternative to the national grid, integrates wastewater treatment systems that meet green standards for reuse, and dedicates ample space for green landscaping. A standout feature is a 50-ha solar farm within the park, reinforcing its commitment to clean energy and environmental responsibility.
The park is also equipped with smart technologies for traffic management, security, and overall operational efficiency, creating a forward-thinking ecosystem for global manufacturers.
VSIP III has already attracted major international companies known for their sustainability commitments – on April 9, Danish toy maker Lego opened its most environmentally friendly factory to date at the complex (see Page 13).
Vietnam has undergone several stages of developing eco-IPs, from the pilot phase in Ninh Binh, Danang, and Can Tho in the 2000s, to replication in localities boasting many IPs, such as in Haiphong, Dong Nai, and Ho Chi Minh City, since 2020.
The nation continues to replicate the models in other localities to promote the national strategy on green growth, the circular economy, and 2050 net-zero commitments.
Paul Tonkes, industrial deputy director Indochina Kajima
All Core5 Vietnam’s properties follow a LEED action plan from construction to operations and management. Our contractors and suppliers are subject to a resource and waste efficiency clause during construction and must prioritise usage of low-energy materials. Our sites are managed to preserve natural habitats and green spaces, minimising disturbance to the local ecological systems.
Core5 is confident that we are well positioned to capture the demand prioritising environmental, social, and governance goals and green production processes. We combine global expertise from Kajima Corporation and Core5 Industrial from the US with exceptional local know-how from Indochina Kajima to create a platform that redefines quality and relationship in Vietnam industrial.
Our assets are carefully crafted following international standards and LEED action plans. Indochina Kajima invests in green production processes for all Core5 Vietnam assets.
All Core5 projects are planned for a full solar rooftop, with vegetation and landscaping to reduce heat islands, optimised ventilation design, health and wellness communal area and installed digital energy metres to monitor and optimise usage. This eco-friendly working environment promotes health and wellbeing for the industrial workforce while significantly reducing operational costs for all Core5 tenants, and helps minimise disturbance to the local biodiversity.
Nha-Vinh Julien Nguyen, country head, WHA Vietnam
WHA owns and manages more than three million square metres of industrial properties and develops 15 industrial zones in Thailand and Vietnam, with a total industrial land of 12,600 hectares.
To attract high value manufacturing investments, WHA industrial zones differentiate with a smart concept based on international standard quality of design and infrastructure, reliability of utilities, and environmental care, integrating use of Industry 4.0 tech.
In Thailand, WHA has been at the forefront of innovation in terms of smart eco features by integrating cutting-edge technology and exploring innovative solutions. These include offering clean energy solutions to industrial customers, including solar rooftop installations with long-term power purchase agreements, piloting peer-to-peer energy trading of excess solar energy using blockchain technology, and recycling wastewater into industrial-grade water.
Additionally, WHA Mobilix is providing logistics operators access to electric vehicle (EV) technology. This is carried out through three main services, covering EV rental, EV charging, and the Mobilix Transportation Optimisation Software Solution, enabling the transition to EVs instead of relying on existing traditional-engine fleets.
Some solutions are already applied in the WHA project in Nghe An province, such as a unique biological wastewater treatment system that does not use chemicals and is environmentally friendly; and a centralised control room that can track and control environmental parameters. More initivates will be implemented in WHA projects in Vietnam in the coming time.
This focus is in line with WHA’s sustainability goals as a developer, and more importantly, to help our industrial customers, the secondary investors, meet their own sustainability goals.
From our observation, there is a clear push for sustainable supply chains. We aim to support and create the most positive outcomes for the surrounding communities while ensuring that the business activities do not negatively impact their living, particularly environmental quality and safety of life. |